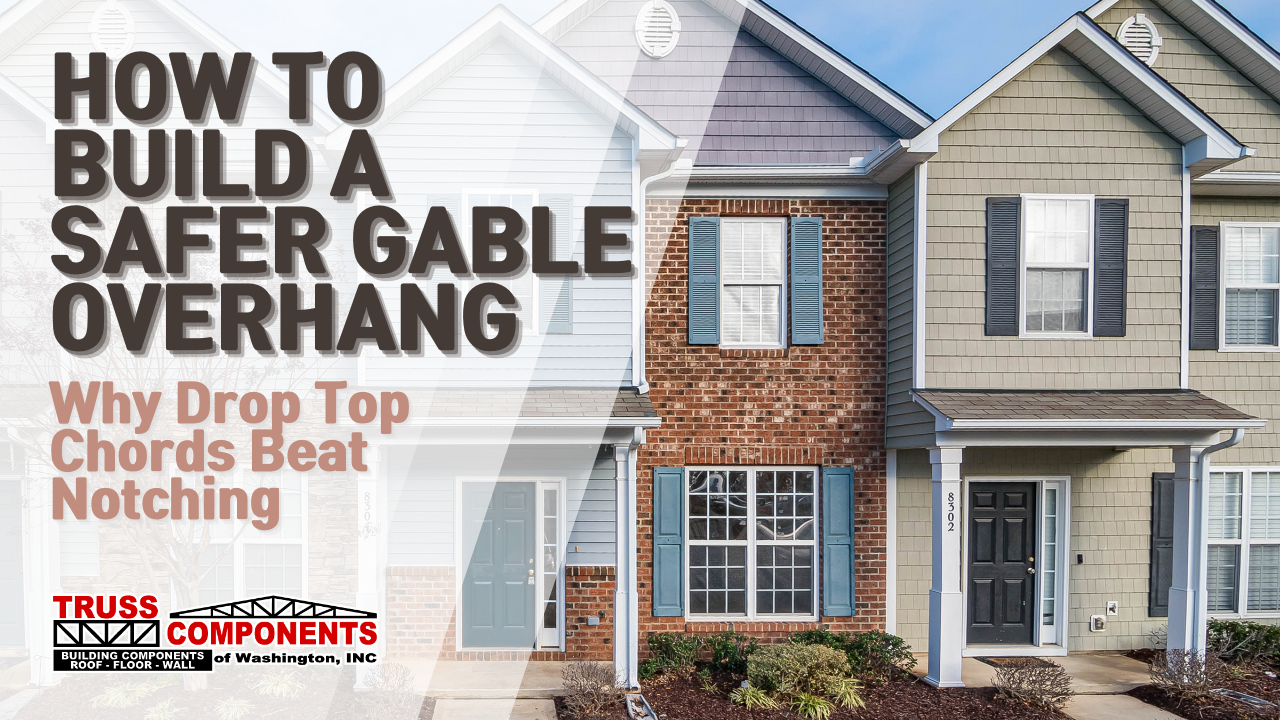
How to Build a Safer Gable Overhang: Why Drop Top Cords Beat Notching
Learn the difference between drop top and notched top cords for gable trusses in this beginner-friendly guide. Discover which method is safer, structurally sound, and easier for siding and soffit installation. Perfect for builders, framers, and anyone working on residential construction projects.
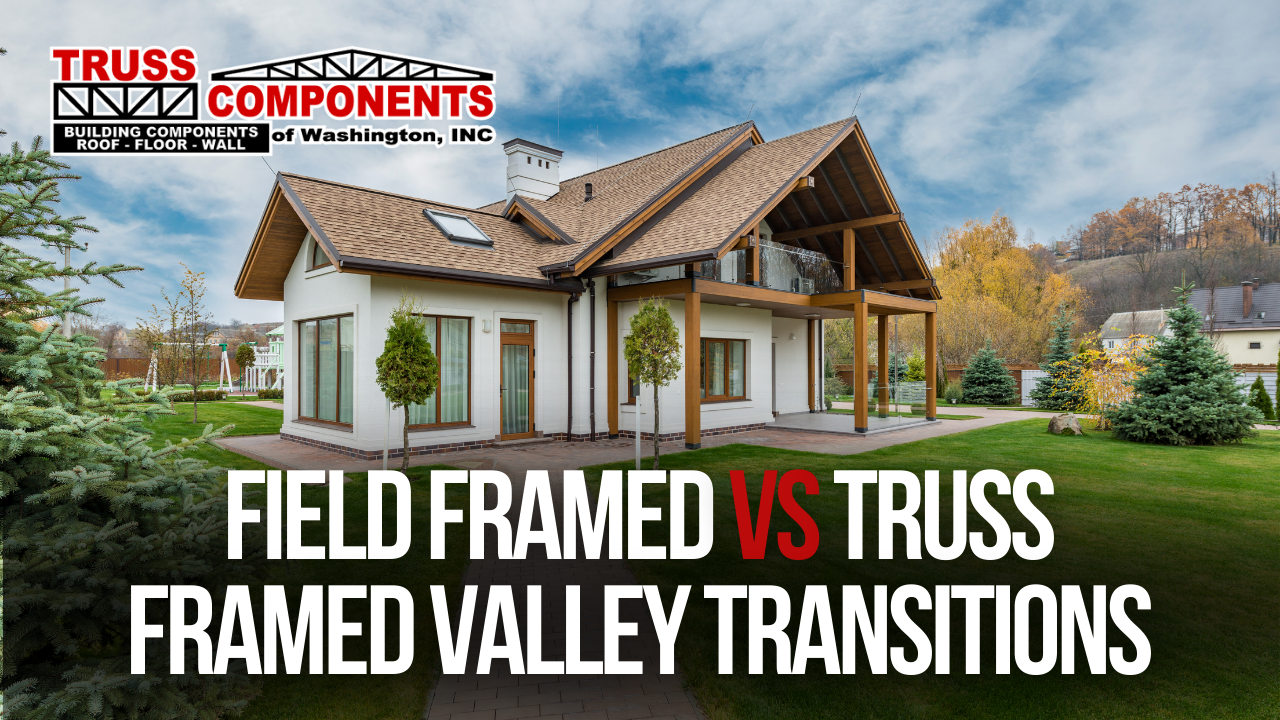
Field Framed vs Truss Framed Valley Transitions
Understand how field framed and truss framed valley transitions affect roof strength, load distribution, and project efficiency. Learn from the experts.
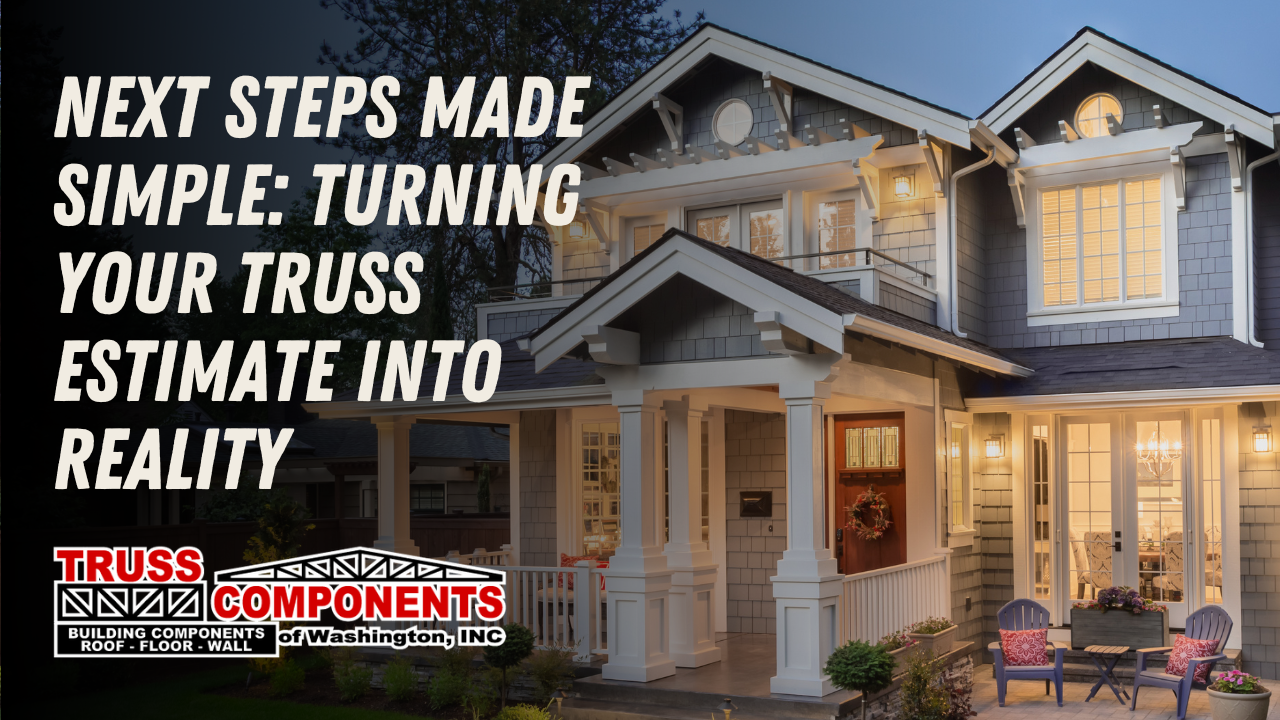
Next Steps Made Simple: Turning Your Truss Estimate into Reality
Truss estimate next steps for contractors: plans, payment, delivery prep, and site support for roof trusses or wall panels.
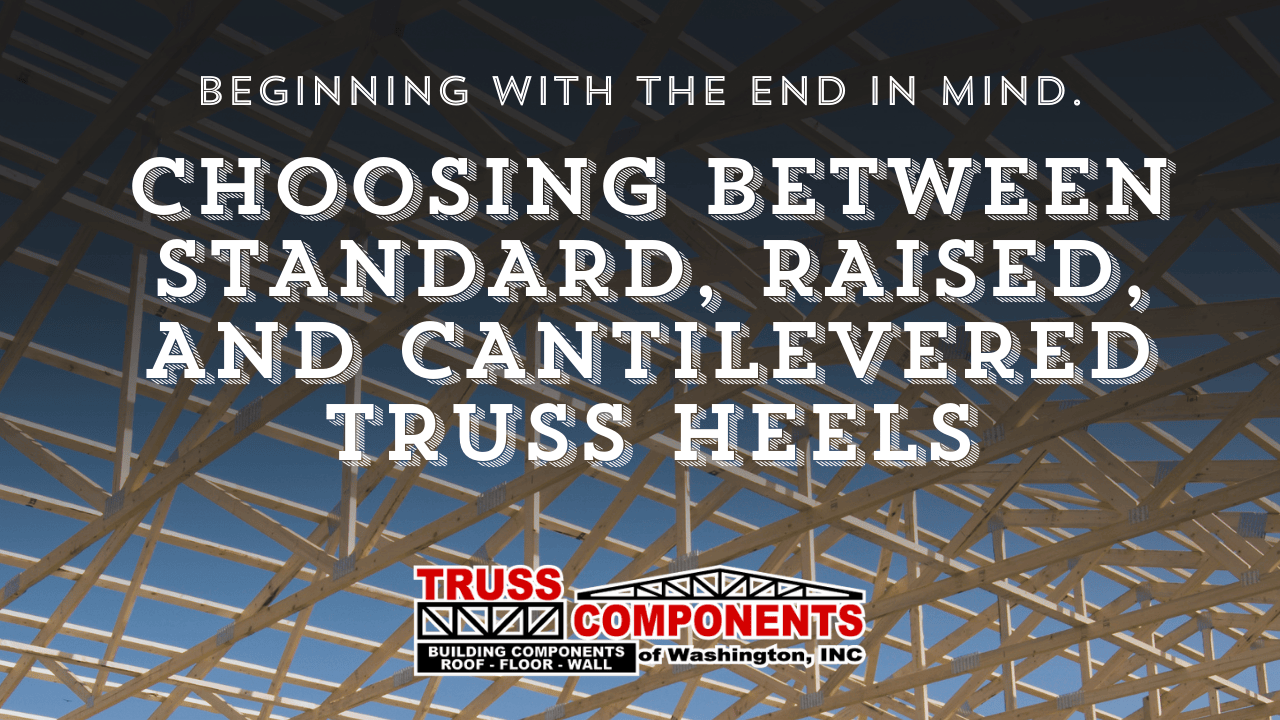
Choosing Between Standard, Raised, and Cantilevered Truss Heels - Beginning with the end in mind.
Learn the pros and cons of standard, raised, and cantilevered truss heels for better roof design, insulation, and attic space.
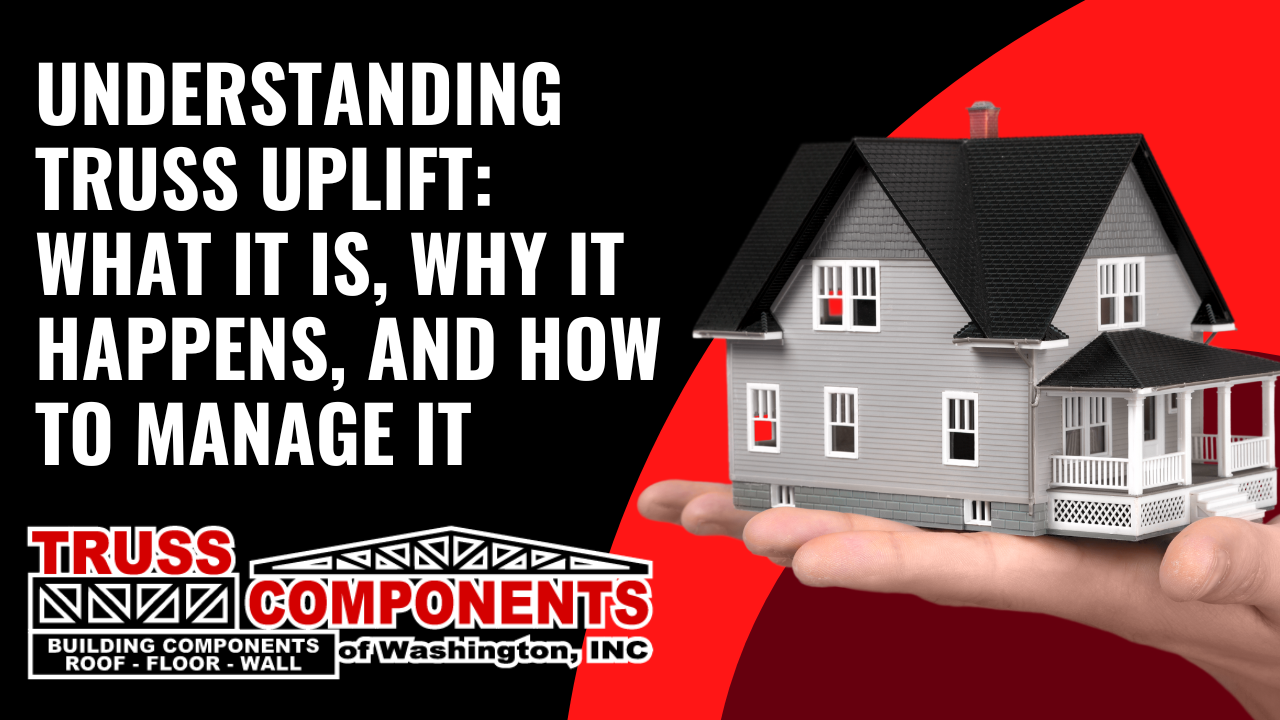
Understanding Truss Uplift: What It Is, Why It Happens, and How to Manage It
Truss uplift, also known as partition separation, is a common and seasonal issue in wood-framed construction. Learn what causes ceiling cracks near interior walls, how moisture and truss design contribute to the problem, and the best practices to minimize cosmetic damage through proper installation and attic ventilation.
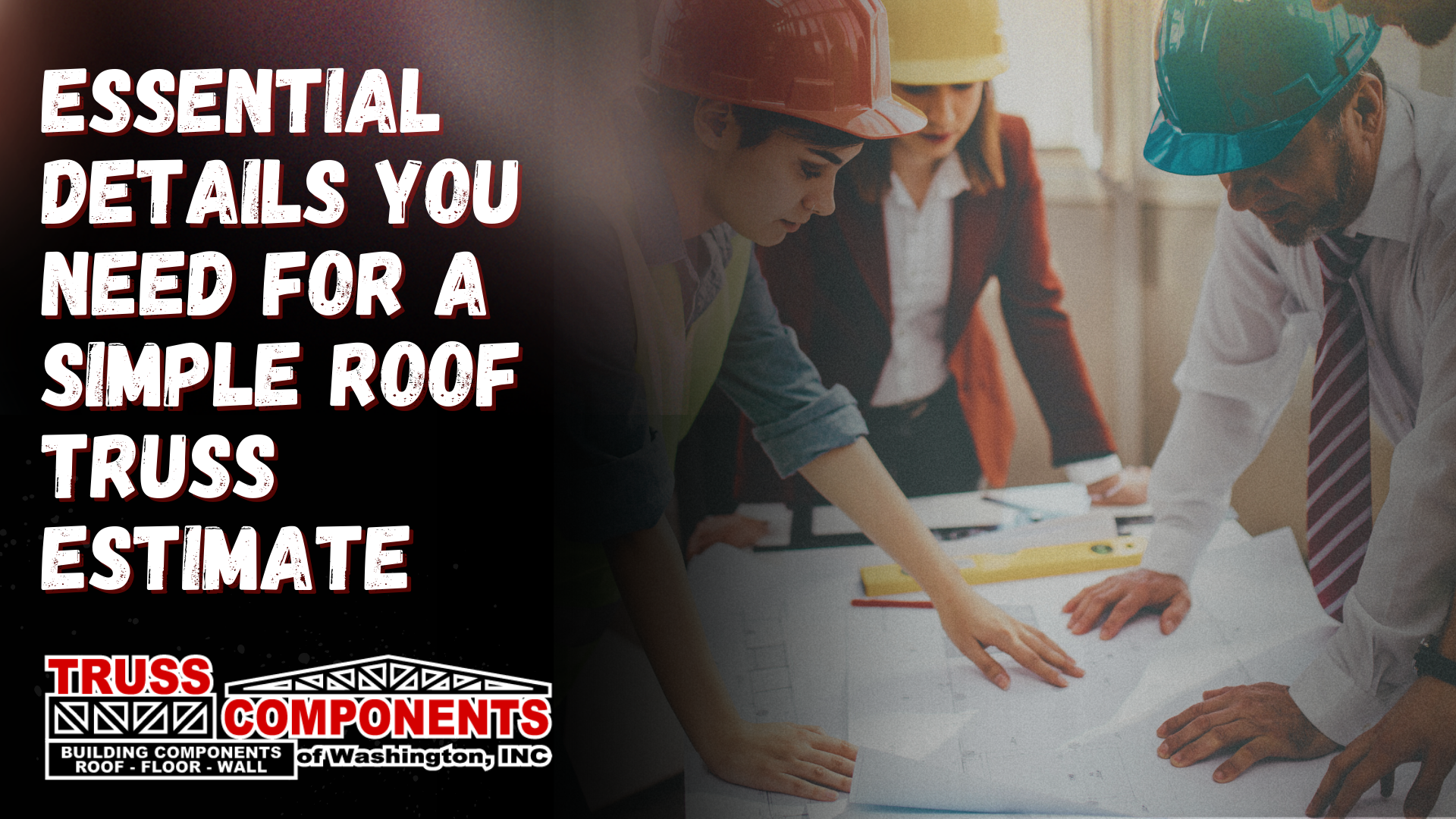
Essential Details You Need for a Simple Roof Truss Estimate
Planning a new build? Make sure your roof truss quote is accurate by providing these essential details. From truss span and spacing to roofing material and building purpose, this guide from Truss Components of Washington explains everything you need to get a fast, reliable estimate for your roof truss package.
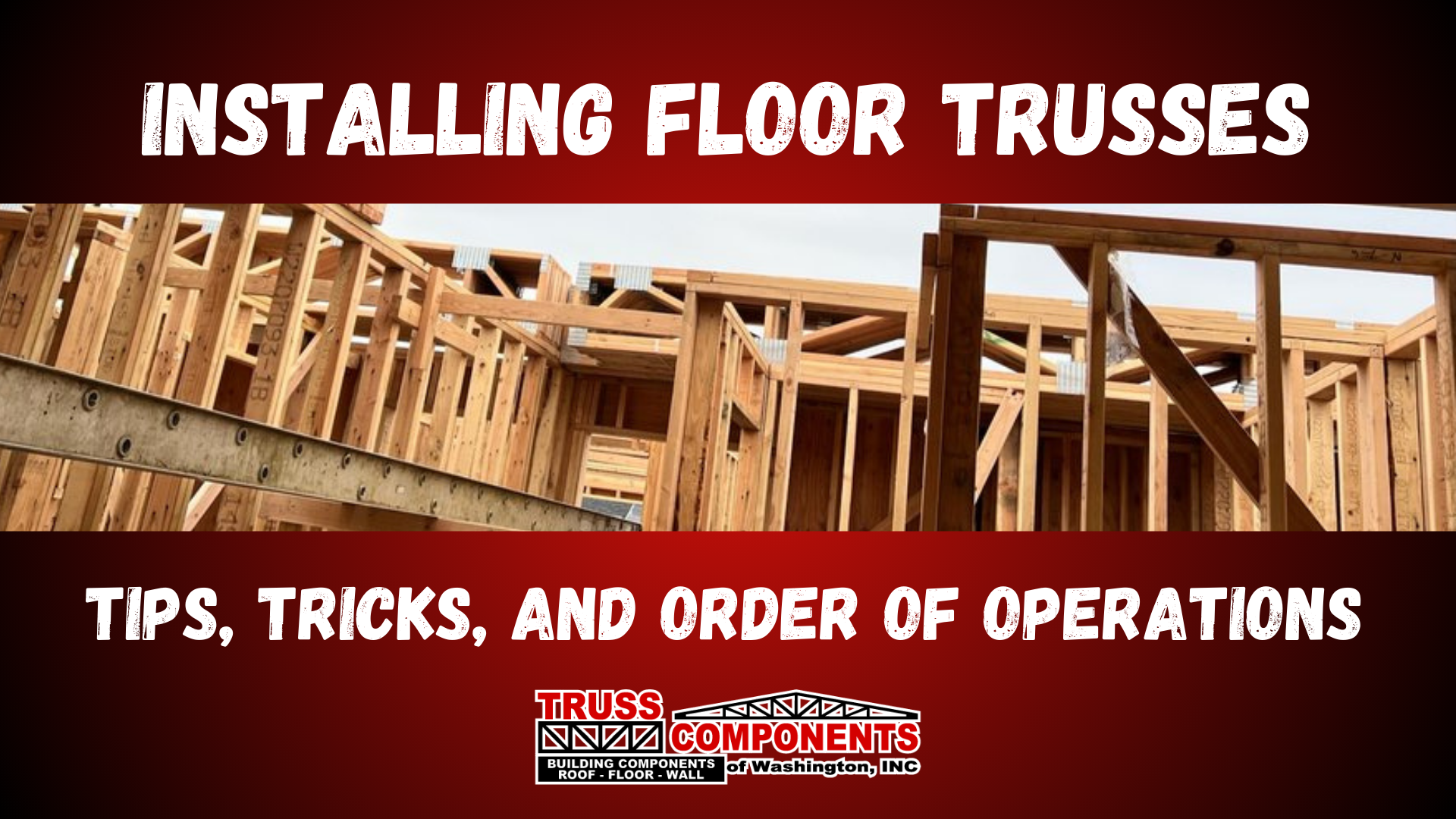
Installing Floor Trusses β Tips, Tricks, and Order of Operations
Learn how to properly install floor trusses with this step-by-step guide. From verifying plans and preparing your site to spacing, bracing, and fastening techniques, this post covers everything builders need for a safe and efficient floor truss installation.
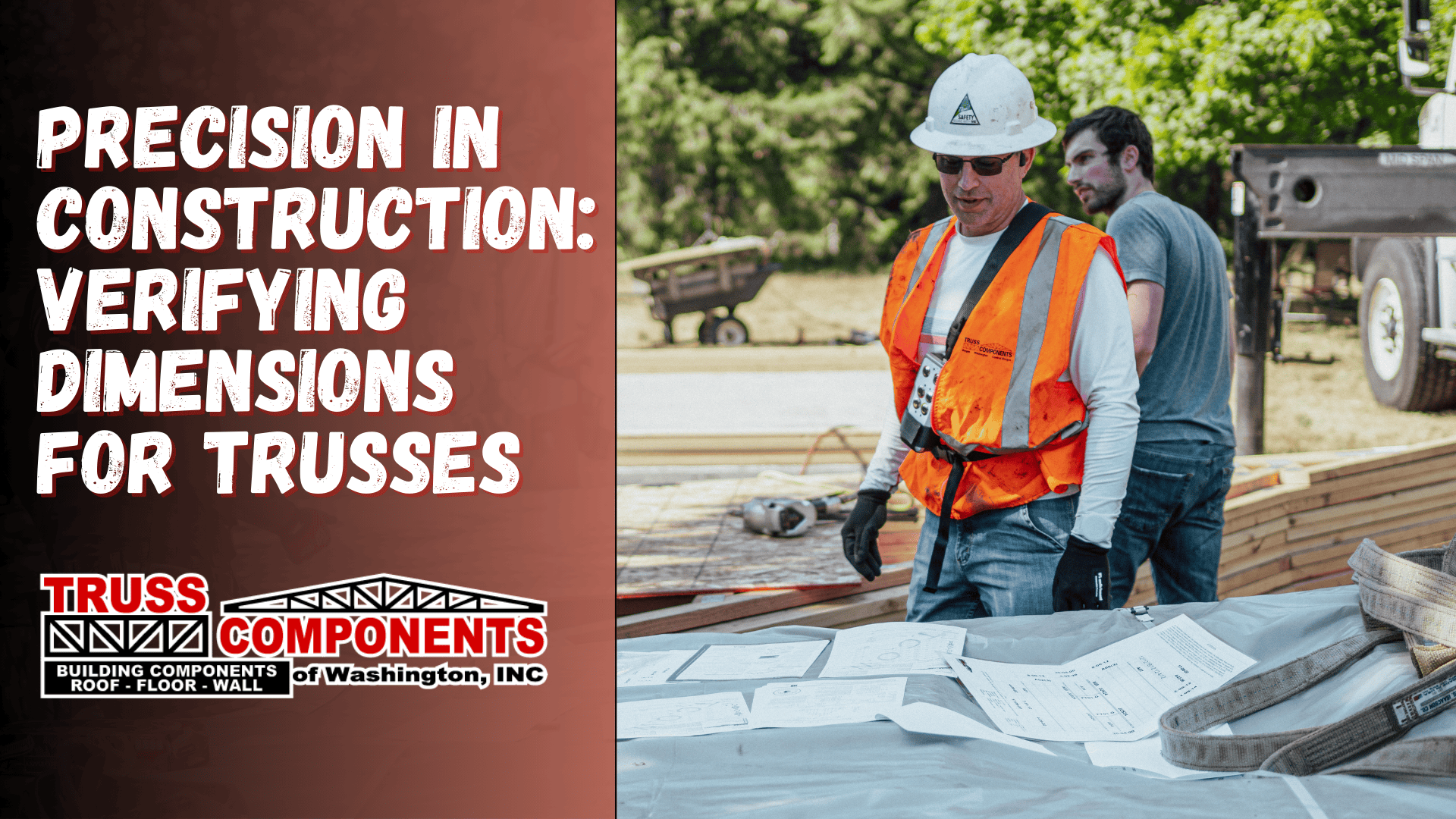
Precision in Construction: Verifying Dimensions for Trusses
Ensure accurate truss measurements for a seamless installation by verifying key dimensions like span, roof pitch, and heel height. Avoid costly modifications and learn how to prepare your site for a smooth truss delivery. πποΈ
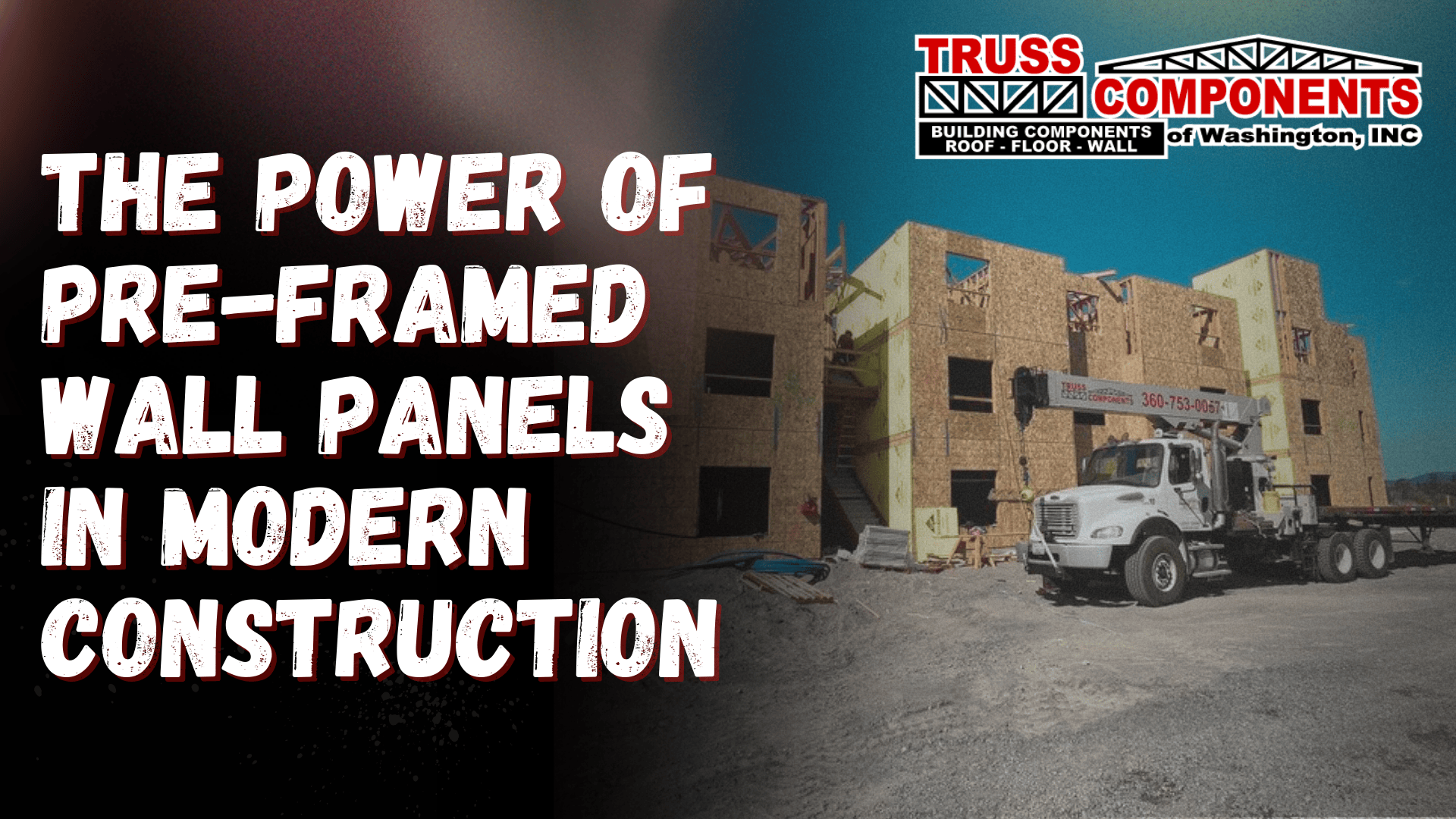
The Power of Pre-Framed Wall Panels in Modern Construction
Pre-framed wall panels are revolutionizing the construction industry by offering a faster, more efficient alternative to traditional on-site framing. Built in a controlled factory environment and delivered ready for installation, these panels reduce labor costs, minimize material waste, and improve job site safety. This article explores the key benefits of pre-framed wall panels, from faster project timelines to enhanced quality control, making them a smart choice for modern builders looking to streamline the framing process.
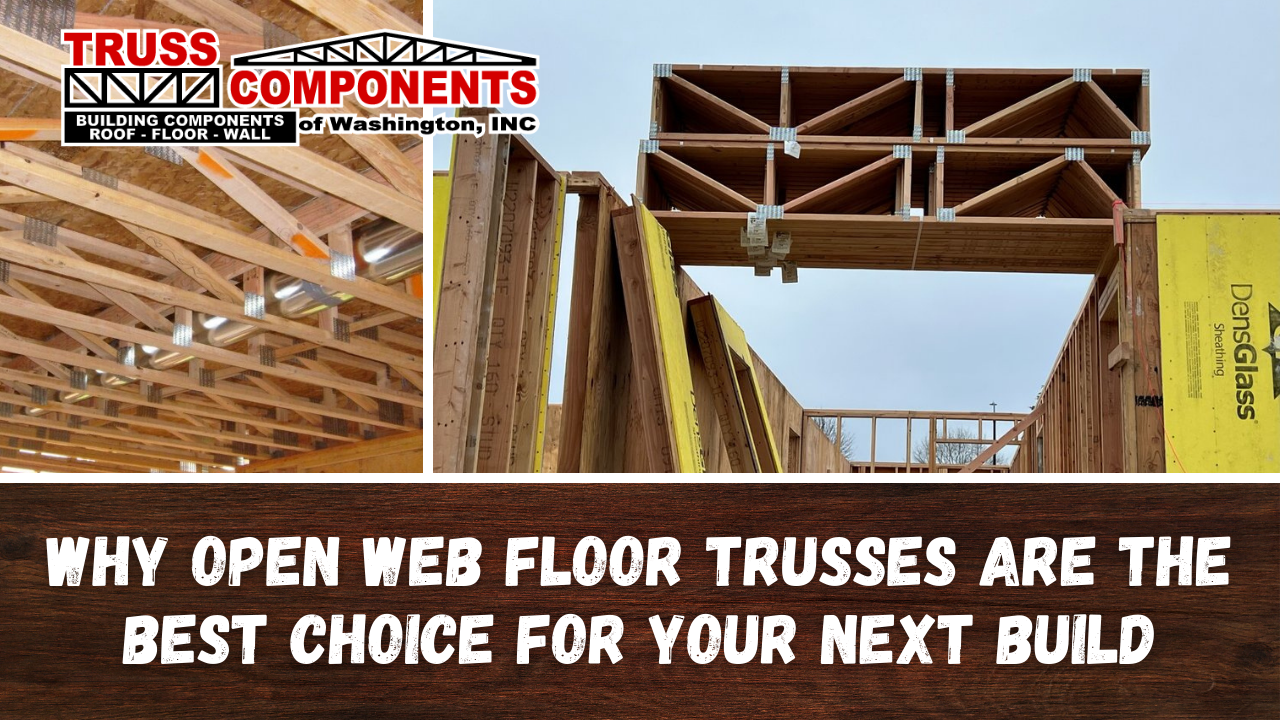
Why Open Web Floor Trusses Are the Best Choice for Your Next Build
Discover why open web floor trusses are the best choice for strength, cost savings, and easy installation in residential and commercial builds.
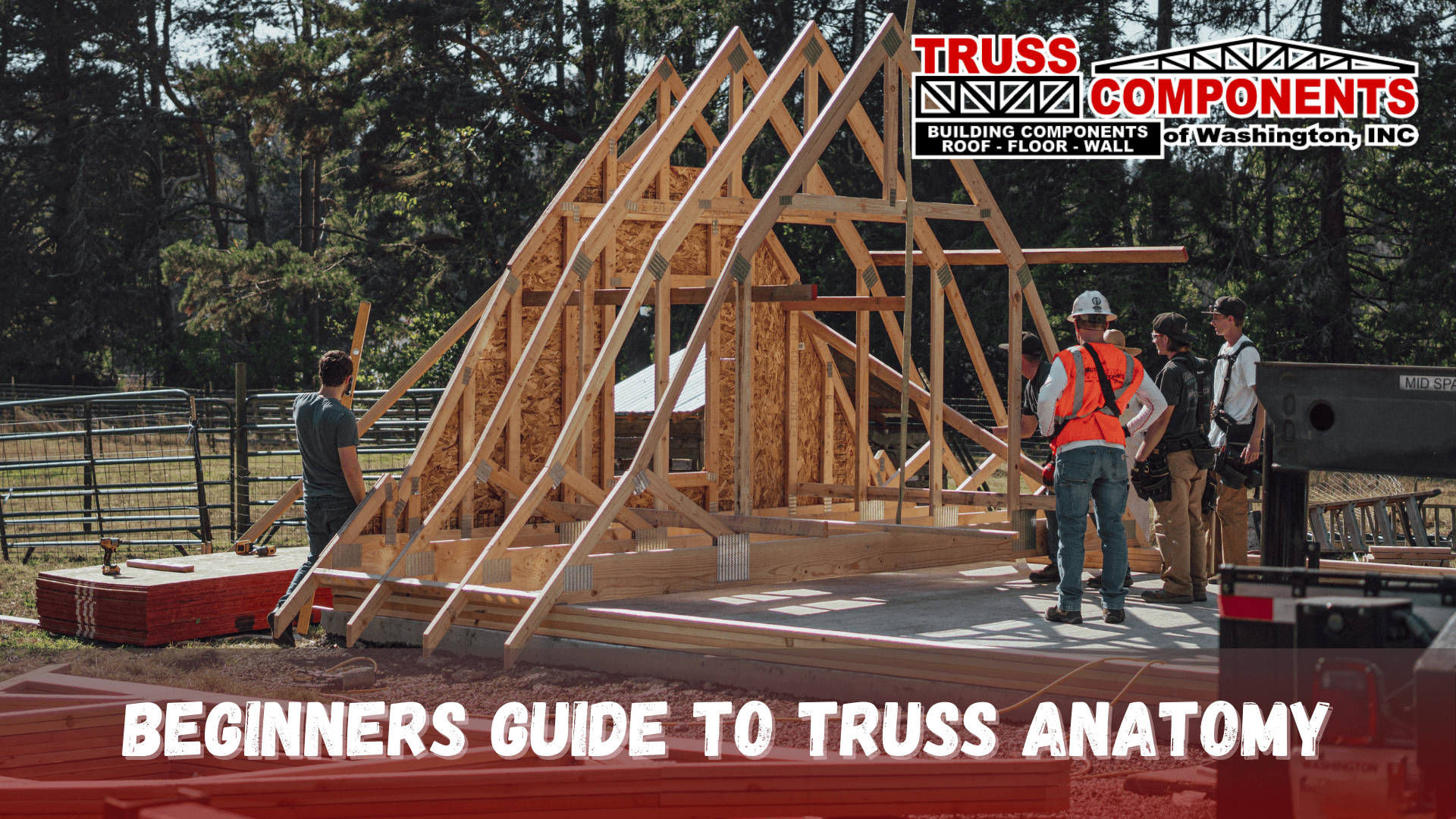
Beginners Guide to Truss Anatomy
Learn the key components of a roof truss, including the top chord, bottom chord, webs, bearing plate, heel height, roof pitch, and overhangs. Discover how proper truss design enhances structural integrity, prevents sagging, improves energy efficiency, and protects your foundation. Whether you're a builder, contractor, or homeowner, understanding truss anatomy is essential for durable and efficient construction.
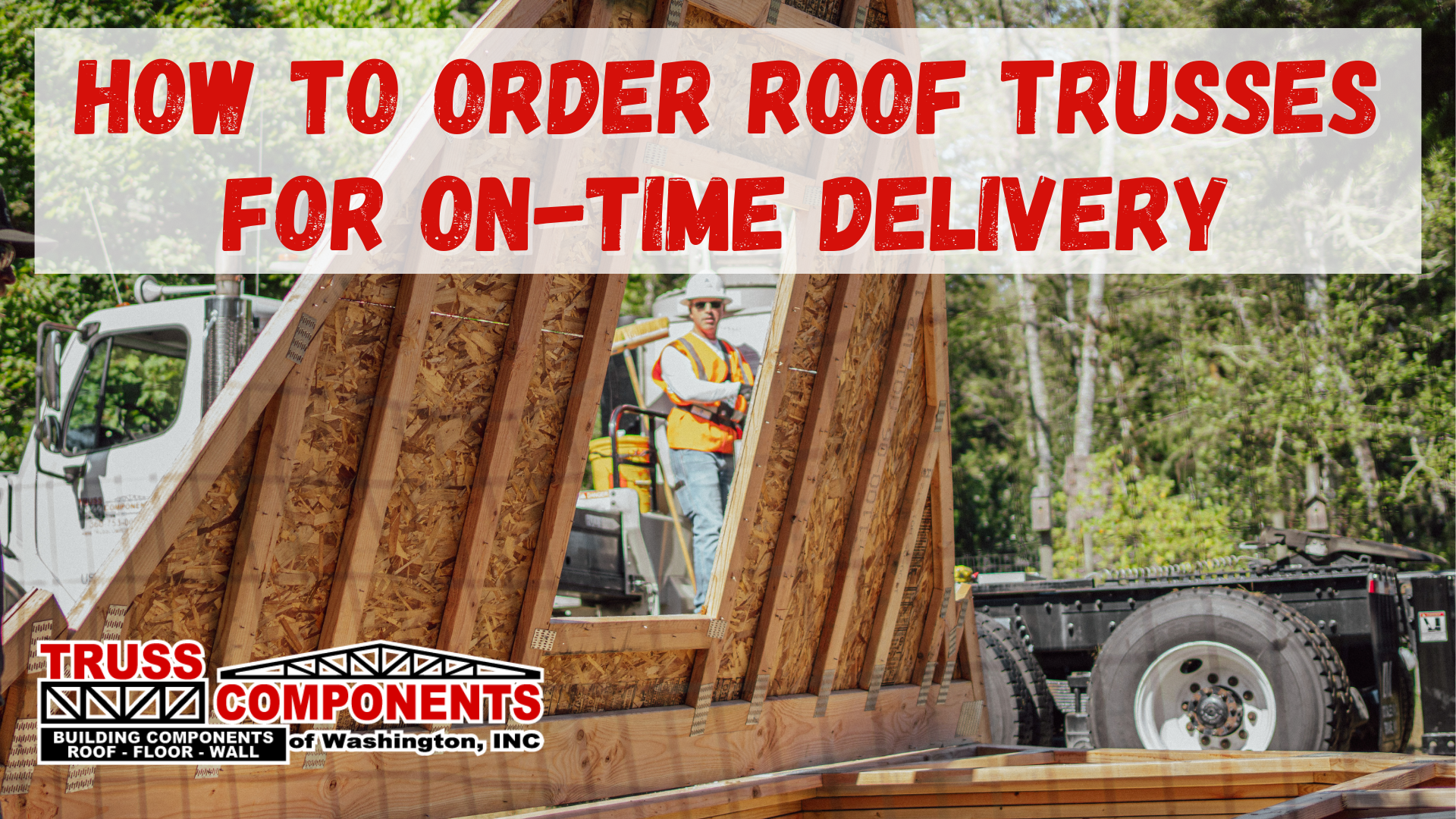
How to Order Roof Trusses for On-Time Delivery
Ordering roof trusses is a crucial step in any construction project, and proper planning can prevent costly delays. This guide walks you through the truss ordering process with Truss Components of WA (TCOW)βfrom working with an architect, submitting your building plans, and finalizing your truss design to scheduling delivery and ensuring a smooth installation. Learn how early communication, site verification, and clear planning can streamline your project and keep everything on schedule.
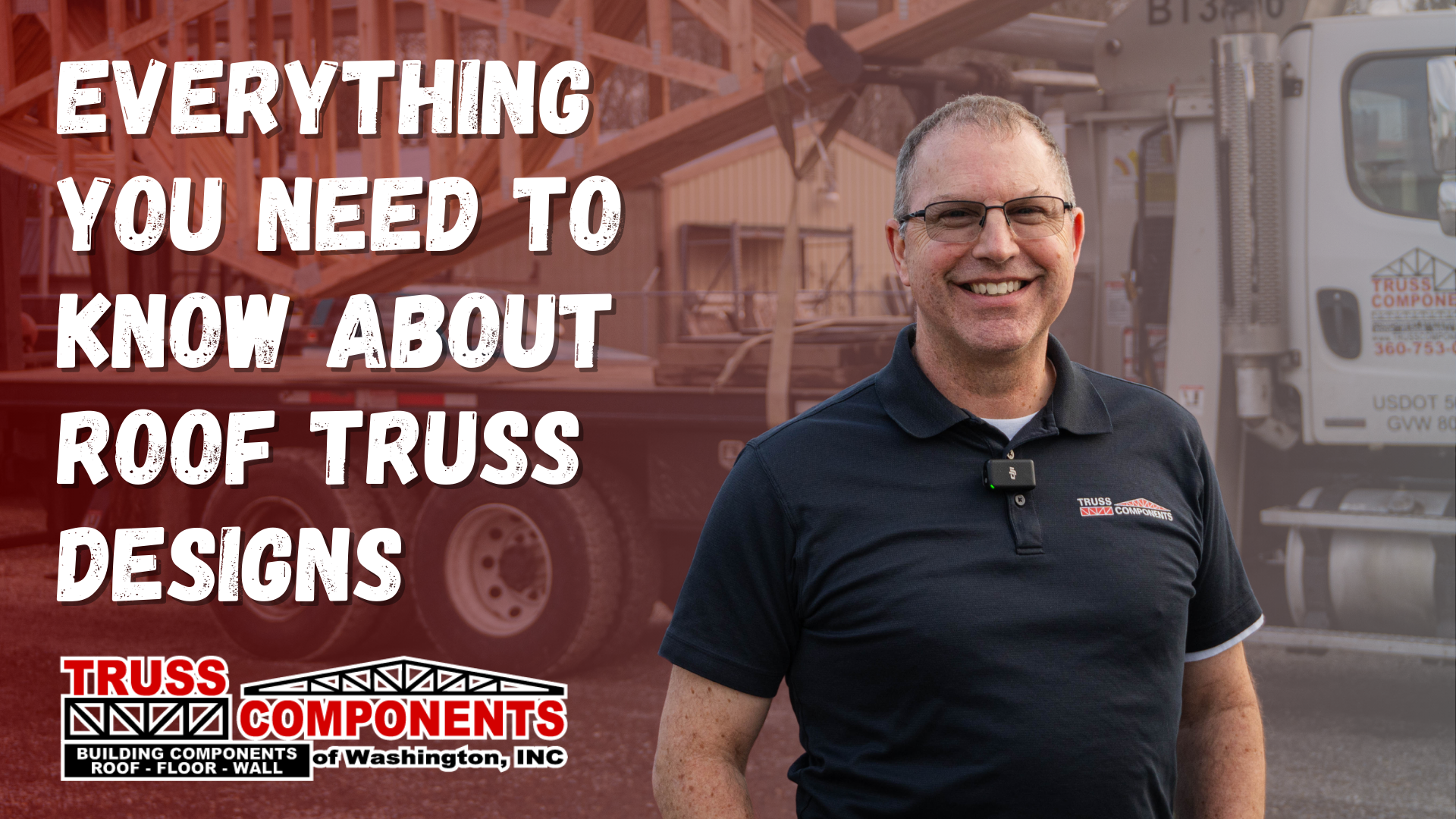
EVERYTHING You Need to Know About Roof Truss Designs
Roof trusses are essential for structural support and design. Common trusses work for most homes, vaulted trusses create open spaces, and mono trusses suit monitor-style buildings. Flat trusses fit modern designs, while room in attic trusses maximize space. Choosing the right truss ensures strength, efficiency, and functionality.
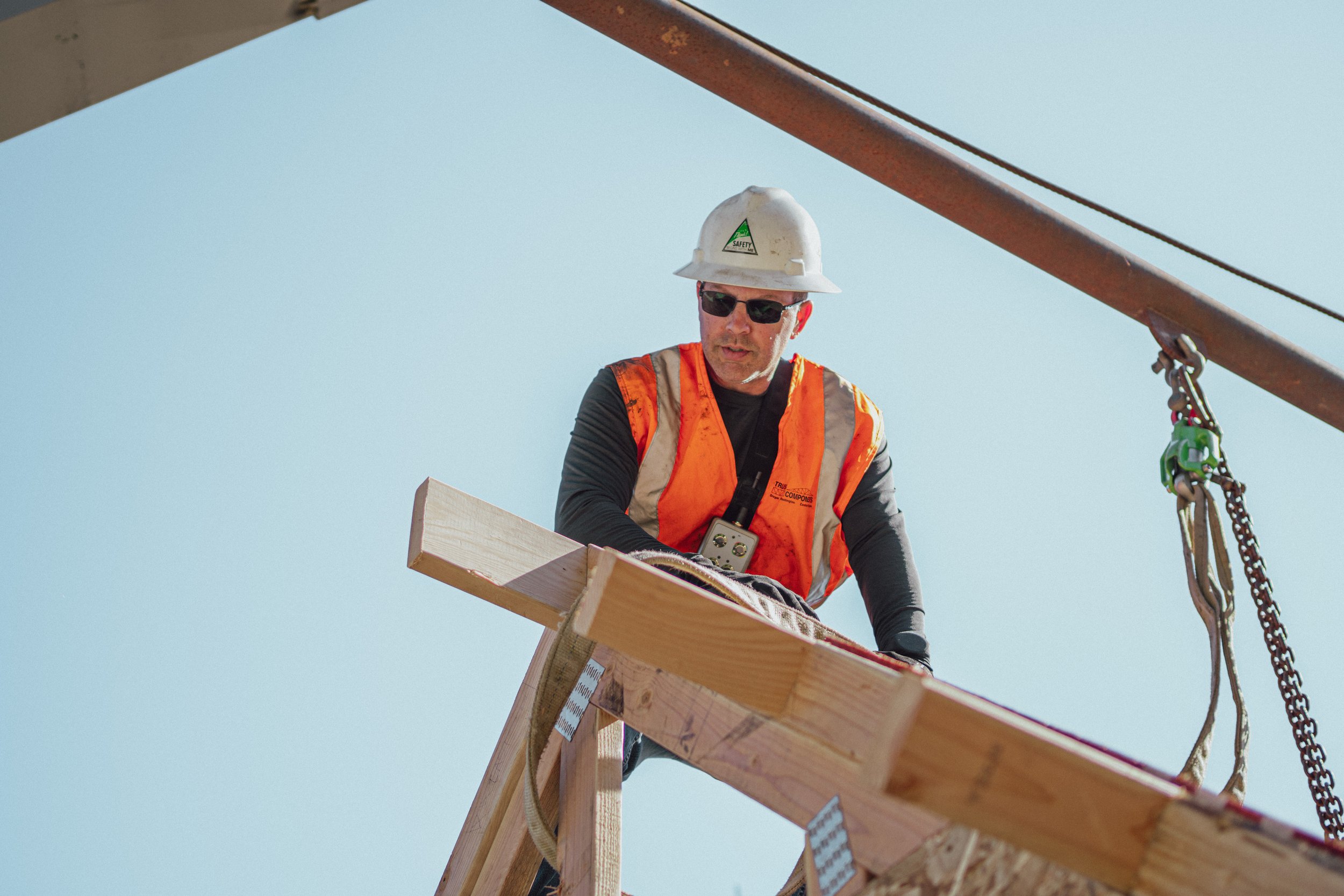
Breaking Down the Costs: What Makes Roof Trusses More Expensive?
Learn what drives roof truss costs and plan your budget with confidence!